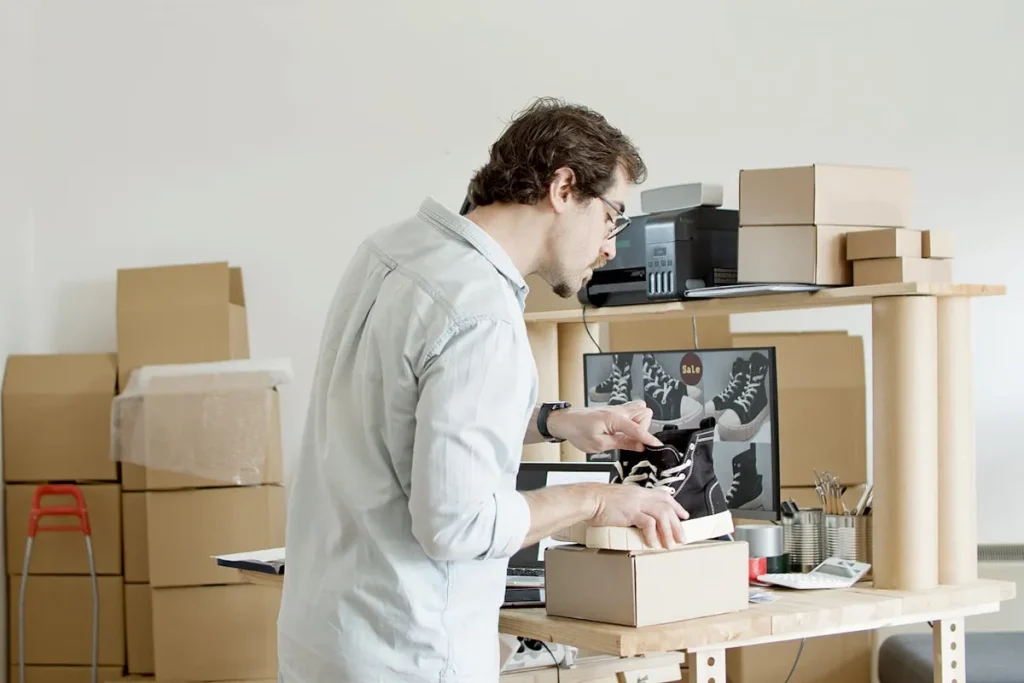
Effective product packaging is a major component of providing a quality product and optimizing your bottom line, far more than just a last step in the production process. Everything from manufacturing speed and material costs to consumer experience and environmental initiatives may be affected by packaging. These five ideas might help you change your strategy and raise general efficiency if you want to simplify your packing procedure without sacrificing quality.
1. Standardize Packaging Materials and Sizes
Reducing the variety of packaging types in your inventory can help you achieve efficiency in your packing operation. Slower assembly, more frequent material changes, and greater waste follow from every product coming in a distinct packaging or using a different filler material. Standardizing your packing materials and sizes whenever feasible helps your team simplify their work and lower their risk of mistakes.
Using uniform box sizes and filling materials makes it easier to implement automation. Consistent inputs help machines applying the tape, inserting items, or printing labels run more smoothly. Along with reducing staff training time, this uniformity simplifies inventory control and storage.
2. Integrate Packaging Design into the Product Development Phase
Many companies view packing as an afterthought—something they consider only once the product is finished. Still, those packaging techniques considered from the start of the product development cycle are the most successful. Designing packaging with the goods allows both to be optimized simultaneously, hence perhaps lowering the weight, size, and shape of the final package.
Additionally resulting from this integration are material and transportation savings. Smaller, lighter items are more easily stored and less expensive to send. Early planning also enables producers to use environmentally friendly materials or look into design ideas meant to increase durability and lower returns from damage. When teams work across departments—manufacturing, marketing, logistics, and product design—packaging becomes a strategic asset rather than only an expense.
3. Use Automation and Technology to Improve Speed and Accuracy
Packaging is being transformed by technology, which also speeds and guarantees reliability more than before. Nowadays, automated technologies may manage jobs including weighing, labeling, taping, and sealing, thereby drastically lowering the necessary manual work. Although automation has an upfront cost, it boosts output, reduces errors, and improves consistency over time.
Software for barcode scanning and tracking can also help to simplify inventory control by guaranteeing fast labeling and packing of the proper products. Robots and conveyor systems can assist in efficiently transporting goods from one station to the next in bigger operations, therefore eliminating bottlenecks and physical worker strain.
Custom software solutions may also be adjusted to track line of performance of packaging, spot slowdowns, and forecast maintenance requirements. These insights let companies change their procedures instantly while maintaining output without expensive downtime.
4. Optimize with Custom Injection Molding Where Appropriate
Investing in customized solutions will save time and raise quality when your packaging demands are specific. Custom injection molding is a wonderful illustration of this as it lets you produce packaging components perfectly to the shape and size of your products. Injection molding is especially useful for making protective inserts, trays, or containers that securely hold goods during transit.
Injection molding frequently yields shorter packaging times and less damaged items, even if it may need an upfront design and tooling cost. Eliminating the need for extra filler or oversized boxes helps manufacturers to use space efficiently as well. The lower material consumption and simplified packing approach over time might result in major cost savings and higher customer satisfaction. Injection molding provides a scalable and safe packaging option for companies transporting delicate, irregular, or valuable items.
5. Train Staff and Continuously Evaluate Your Process
Even the most advanced packaging system won’t be effective without a well-trained team. Make sure every employee engaged in packaging is familiar with the tools, knows best practices, and can identify problems before they grow to be more significant ones. Faster, more precise, and more able to adjust to changes in packaging needs a well-trained team to be.
Apart from instruction, develop the practice of routinely analyzing your packing technique. Track shipment damage rates, review package waste and get feedback from the floor. Little modifications like changing tape manufacturers, modifying box dimensions, or repositioning a workstation might, over time, add up to significant gains.
By evaluating performance across shifts and product lines using data analytics tools, you may also spot trends and guide your decisions on where to concentrate efforts at improvement.
Conclusion
Improving product packaging is about establishing a system that balances speed, quality, cost, and customer happiness rather than only about speeding things up. Standardizing materials, planning ahead of time, adopting technology, looking into custom solutions like injection molding, and always personnel training can help you create a packaging process that matches your more general corporate objectives. Efficient packaging is more than a small detail; it’s a competitive advantage. Therefore, your approach to packing should change as production does.